ထိုးပြီး အထည်များ ထုတ်လုပ်ခြင်း လုပ်ငန်းစဉ်
တရုတ်အထည် စက်ရုံအဖြစ် ပြောမှာknitted အထည်များနှင့်ချည်ထည်s၊ Shaoxing Starke သည် သုံးစွဲသူများအား အရည်အသွေးမြင့် အထည်ဖြေရှင်းနည်းများ ပေးအပ်ရန် ကတိပြုပါသည်။ ယနေ့တွင်၊ ကျွန်ုပ်တို့သည် ချည်သားထုတ်လုပ်ခြင်းမှ ကုန်ချောထုတ်ခြင်းအထိ ကဏ္ဍပေါင်းစုံကို လွှမ်းခြုံထားသော ကျွန်ုပ်တို့၏ အထည်ထုတ်လုပ်ခြင်းလုပ်ငန်းစဉ်ကို နက်ရှိုင်းစွာ နားလည်သဘောပေါက်ရန် သင့်အား ခံယူပါမည်။ ကျွန်ုပ်တို့၏လုပ်ငန်းစဉ်တွင် အဓိကအဆင့်ငါးဆင့်ပါဝင်သည်- ချည်ထုတ်လုပ်ခြင်း၊ ယက်လုပ်ခြင်း၊ ဆေးဆိုးခြင်း၊ အချောထည်ပြုလုပ်ခြင်းနှင့် ထုတ်ကုန်အချောထည်ပြုလုပ်ခြင်းတို့ဖြစ်သည်။ ဤကောင်းမွန်သော လုပ်ငန်းစဉ်များမှတစ်ဆင့် အထည်၏မီတာတိုင်းသည် ကျွန်ုပ်တို့၏ဖောက်သည်များ၏ လိုအပ်ချက်နှင့် မျှော်လင့်ချက်များကို ဖြည့်ဆည်းပေးနိုင်ကြောင်း သေချာပါသည်။ တီထွင်ဖန်တီးမှုနှင့် နည်းပညာအပြည့်ဖြင့် ဤခရီးကို အတူတကွ စူးစမ်းကြည့်ကြပါစို့။
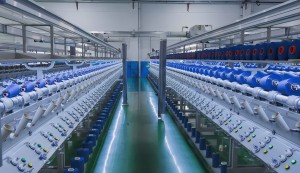
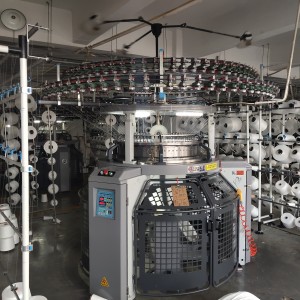
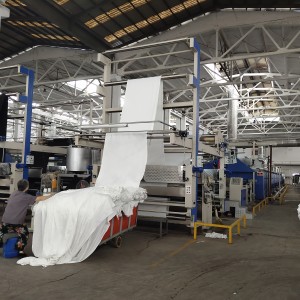
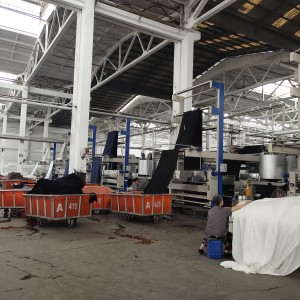
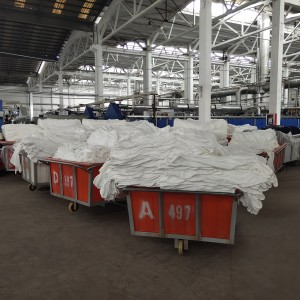
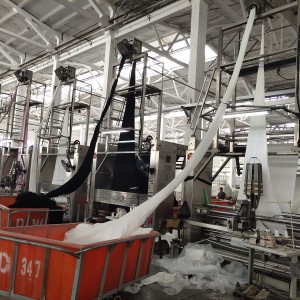
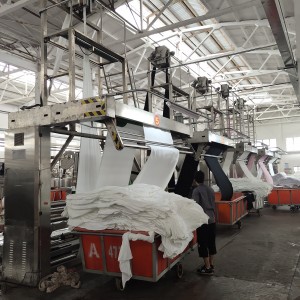
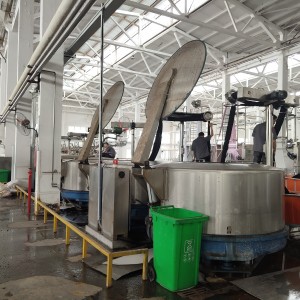
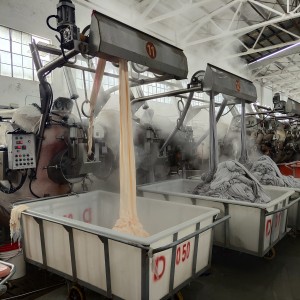
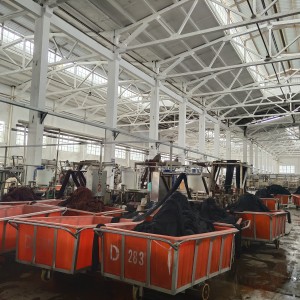
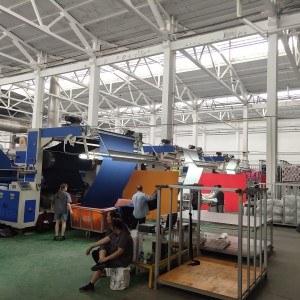
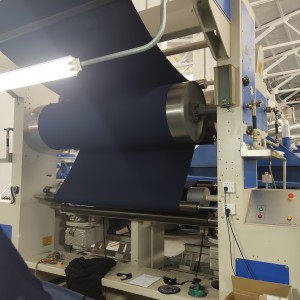
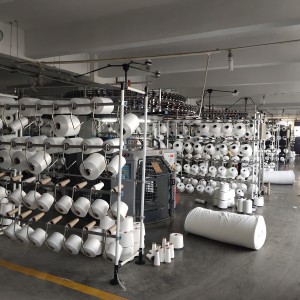
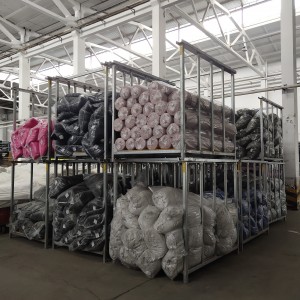
1. ချည်မျှင်ကိုထုတ်လုပ်ပါ။
ချည်ထည်များပြုလုပ်ရာတွင် ပထမအဆင့်မှာ ချည်မျှင်များထုတ်လုပ်ခြင်းဖြစ်ပြီး ချည်ထည်များ၏အရည်အသွေးသည် အသုံးပြုထားသောချည်များပေါ်တွင် တိုက်ရိုက်မူတည်သောကြောင့် အရေးကြီးသောလုပ်ငန်းစဉ်တစ်ခုဖြစ်သည်။ ချည်ထည်များ၏ ကုန်ကြမ်းများကို အဓိကအားဖြင့် ချည်သားစစ်စစ်၊ polyester၊ သိုးမွှေး၊ ပိုးထည်စသည့် ပစ္စည်းအမျိုးမျိုးဖြင့် ပြုလုပ်ထားပြီး စံပြခံစားမှုနှင့် စွမ်းဆောင်ရည်ရရှိရန် သင့်လျော်သောအချိုးအစားဖြင့် ရောစပ်ထားသည်။ ဥပမာအားဖြင့်၊ ချည်သားစစ်စစ်သည် လေဝင်လေထွက်ကောင်းပြီး သက်တောင့်သက်သာရှိကာ polyester သည် ပိုခိုင်ခံ့သော ဝတ်ဆင်မှုနှင့် အရေးအကြောင်းများကို ခံနိုင်ရည်ရှိသော်လည်း သိုးမွှေးသည် နွေးထွေးမှုကို တိုးစေပြီး ပိုးသားသည် အထည်ကို တောက်ပြောင်ချောမွေ့စေသည့် ခံစားချက်ကိုပေးပါသည်။ ထို့ကြောင့် မှန်ကန်သော ကုန်ကြမ်းနှင့် ရောစပ်အချိုးအစားကို ရွေးချယ်ခြင်းသည် အရည်အသွေးမြင့် ချည်ထည်များ ပြုလုပ်ရန် သော့ချက်ဖြစ်သည်။
ချည်၏ထုတ်လုပ်မှုလုပ်ငန်းစဉ်တွင်၊ ချည်၏အရည်အသွေးသည် နောက်ဆုံးထုတ်ကုန်၏အရည်အသွေးနှင့် စွမ်းဆောင်ရည်ကို တိုက်ရိုက်အကျိုးသက်ရောက်သောကြောင့် အရည်အသွေးထိန်းချုပ်မှုသည် အထူးအရေးကြီးပါသည်။ ချည်၏အရည်အသွေးကောင်းမွန်မှုကို သေချာစေရန်အတွက် ထုတ်လုပ်မှုလုပ်ငန်းစဉ်သည် နူးညံ့သိမ်မွေ့သောလုပ်ငန်းစဉ်များ ဆက်တိုက်လုပ်ဆောင်ရန် လိုအပ်ပါသည်။ ဤလုပ်ငန်းစဉ်များတွင် ဝါဂွမ်းရွေးချယ်ခြင်း၊ အဖွင့်၊ ပုံဆွဲခြင်း၊ ဖြီးခြင်း၊ လှည့်ပတ်ခြင်းနှင့် ချည်မျှင်စသည်တို့ ပါဝင်သည်။
ပထမဦးစွာ၊ ဝါဂွမ်းရွေးချယ်မှုသည် ကုန်ကြမ်းများ၏ သန့်ရှင်းစင်ကြယ်စေရန်အတွက် ကြီးမားသော ချည်မျှင်များမှ အရည်အသွေးမြင့် ချည်မျှင်များကို ရွေးချယ်ရန်၊ အညစ်အကြေးများနှင့် ညံ့ဖျင်းသော ဝါဂွမ်းများကို ဖယ်ရှားရန် ဖြစ်သည်။ ထို့နောက် ဖွင့်လှစ်ခြင်းလုပ်ငန်းစဉ်သည် ချည်မျှင်များကိုဖွင့်ရန်နှင့် နောက်ဆက်တွဲလုပ်ဆောင်မှုအတွက် လျော့ရဲသွားစေရန် စက်ကိရိယာများကို အသုံးပြုသည်။ ထို့နောက် ပုံဆွဲခြင်းလုပ်ငန်းစဉ်တွင် ချည်မျှင်အများအပြားကို ချည်သား၏တူညီမှုနှင့် ခိုင်ခံ့မှုတိုးတက်စေရန်အတွက် ယူနီဖောင်းချည်အမြှောင်တစ်ခုအဖြစ် ပေါင်းစပ်ထားသည်။
ဖြီးခြင်းလုပ်ငန်းစဉ်သည် ချည်သား၏ချောမွေ့မှုနှင့် ခိုင်ခံ့မှုကို ပိုမိုတိုးတက်ကောင်းမွန်လာစေရန်အတွက် ချည်မျှင်တိုတောင်းသော အမျှင်များနှင့် အညစ်အကြေးများကို ဖယ်ရှားရန် အထူးဖြီးပေးသည့်ကိရိယာကို အသုံးပြုပါသည်။ ဖြီးပြီးနောက်၊ ချည်သားသည် အများအားဖြင့် ပိုမိုနူးညံ့ပြီး အဆင့်မြင့် ချည်ထည်များကို ပြုလုပ်ရန် သင့်လျော်ပါသည်။ နောက်ပိုင်းတွင်၊ ချည်မျှင်နှင့် ပတ်ချာလည်ချည်မျှင်များ ထုတ်လုပ်မှုသည် မတူညီသော ချည်ထည်များ၏ လိုအပ်ချက်များကို ဖြည့်ဆည်းပေးရန်အတွက် အမျိုးမျိုးသော အထူရှိသော ချည်မျှင်များဖြစ်အောင် ပေါင်းထားသော ချည်မျှင်များကို လှည့်ပတ်ရန်ဖြစ်သည်။
2.Fabric ယက်လုပ်ခြင်း။
ချည်မျှင်ထုတ်လုပ်မှုပြီးစီးပြီးနောက် နောက်တစ်ဆင့်မှာ ထုတ်လုပ်မှုလုပ်ငန်းစဉ်တစ်ခုလုံးအတွက် အရေးကြီးသောအဆင့်ဖြစ်သည့် အထည်ရက်လုပ်ခြင်းဖြစ်ပါသည်။ သိုးမွှေးထိုးထည်ထုတ်လုပ်ခြင်း၏ အဓိကလင့်ခ်အဖြစ် သိုးမွှေးထိုးအပ်နည်းပညာ၊ အပ်ထိုးအပ်အရေအတွက်၊ သိုးမွှေးထိုးစက်မော်ဒယ်များ၊ သိုးမွှေးထိုးနည်းများ စသည်တို့အပါအဝင် ကဏ္ဍပေါင်းစုံပါဝင်ပါသည်။ ဤအချက်များသည် ထုတ်လုပ်မှုစွမ်းဆောင်ရည်ကို ထိခိုက်စေရုံသာမက နောက်ဆုံးထုတ်ကုန်၏ အရည်အသွေး၊ အသွင်အပြင်နှင့် ခံစားမှုတို့နှင့်လည်း တိုက်ရိုက်သက်ဆိုင်ပါသည်။
ပထမဦးစွာ၊ ချည်ထိုးအပ်များ၏ရွေးချယ်မှုသည်ထည်၏သိပ်သည်းဆနှင့်အထူကိုအကျိုးသက်ရောက်လိမ့်မည်။ အပ်များများလေလေ၊ အထည်ပိုတင်းလာလေလေ၊ ခံစားချက်ပို၍ သိမ်မွေ့လေလေ၊ အပ်အနည်းငယ်ပါသော အထည်များသည် လေ၀င်လေထွက်ကောင်းစေပြီး နွေရာသီအဝတ်အစားလိုအပ်ချက်များအတွက် သင့်လျော်ပါသည်။ ဒုတိယအနေဖြင့်၊ မတူညီသော ချည်ထိုးစက်မော်ဒယ်များသည် အထည်၏ဝိသေသလက္ခဏာများပေါ်တွင် သိသာထင်ရှားသော သက်ရောက်မှုရှိမည်ဖြစ်သည်။ ခေတ်မီ ချည်ထိုးစက်များသည် များသောအားဖြင့် ပိုမိုတိကျပြီး ထိရောက်မှုရှိပြီး စျေးကွက်၏ စိတ်ကြိုက်ဖန်တီးမှုနှင့် ကွဲပြားမှုများအတွက် စျေးကွက်၏လိုအပ်ချက်ကိုဖြည့်ဆည်းရန်အတွက် ပိုမိုရှုပ်ထွေးသောပုံစံများနှင့် ဒီဇိုင်းများကို ထုတ်လုပ်နိုင်သည်။
ထို့အပြင်၊ ချည်ထိုးနည်းလမ်းရွေးချယ်မှုသည်အညီအမျှအရေးကြီးသည်။ ချည်ထိုးနည်းများတွင် ပြားချပ်ချပ်ထိုးအပ်များ၊ ဖဲကြိုးထိုးအပ်များ၊ ကွင်းထိုးအပ်များ စသည်တို့ပါဝင်ပြီး ၎င်းတို့တစ်ခုစီသည် အထည်၏ မတူညီသော elasticity နှင့် ပုံပန်းသဏ္ဌာန်အကျိုးသက်ရောက်မှုကိုပေးသည်။ ဥပမာအားဖြင့်၊ အနီးကပ်လိုက်ဖက်သောအဝတ်အစားများပြုလုပ်ရန်သင့်လျော်သော ၎င်းတို့၏ထူးခြားသောဖွဲ့စည်းပုံကြောင့် ribbed knitted fabrics များသည် ကောင်းမွန်သော elasticity နှင့် recovery ရှိသည်။ ဆောင်းရာသီအဝတ်အစားအတွက် သင့်လျော်သော လေးလံသောအထည်များပြုလုပ်ရန် ကြိုးကွင်းအပ်များကို အသုံးပြုကြသည်။
ယက်လုပ်ပြီးနောက်၊ အထည်သည် နောက်ဆုံးထုတ်ကုန်မဟုတ်သော်လည်း နှစ်မြှုပ်ခြင်း၊ ဆေးဆိုးခြင်း စသည်တို့ကို ဆက်တိုက်လုပ်ဆောင်ရန် လိုအပ်ပါသည်။ ဤလုပ်ငန်းစဉ်များသည် အထည်၏အရောင်အသွေးနှင့် အမြင်အာရုံကို မြှင့်တင်ပေးနိုင်ရုံသာမက အထည်၏ကြာရှည်ခံမှုနှင့် သက်တောင့်သက်သာရှိမှုကိုလည်း မြှင့်တင်ပေးနိုင်ပါသည်။ နှစ်မြှုပ်ခြင်း လုပ်ငန်းစဉ်သည် အထည်ရှိ အညစ်အကြေးများကို ဖယ်ရှားနိုင်ပြီး အထည်၏ သန့်ရှင်းမှုကို သေချာစေပြီး ဆေးဆိုးခြင်း လုပ်ငန်းစဉ်သည် အထည်အား ကြွယ်ဝသော အရောင်များကို ပေါင်းထည့်ကာ စျေးကွက်တွင် ပြိုင်ဆိုင်မှု ပိုမိုစေသည်။
၃။ဆေးဆိုးခြင်းနှင့် ပြုပြင်ခြင်း။
ထိုးပြီးသောအထည်များ၏ dyeing process သည် အတော်လေးရှုပ်ထွေးပြီး နည်းပညာအရ တောင်းဆိုသည့်လုပ်ငန်းစဉ်ဖြစ်ပြီး အချက်များစွာကို ကျယ်ကျယ်ပြန့်ပြန့် ထည့်သွင်းစဉ်းစားပါသည်။ ပထမဦးစွာ၊ ဆိုးဆေး၏ရွေးချယ်မှုသည် ကွဲပြားခြားနားမှုအပေါ် အခြေခံရပါမည်။အထည်ပစ္စည်းများ. ဥပမာအားဖြင့်၊ ချည်ထိုးထားသောအထည်များသည် များသောအားဖြင့် တိုက်ရိုက်ဆိုးဆေးအတွက် သင့်လျော်ပြီး သိုးမွှေး သို့မဟုတ် ပိုးကဲ့သို့သော သဘာဝအမျှင်များသည် အက်ဆစ်ဆိုးဆေးအတွက် ပိုသင့်လျော်ပါသည်။ အဘယ်ကြောင့်ဆိုသော် မတူညီသော ဆိုးဆေးများတွင် အမျှင်များနှင့် ကွဲပြားသော ဆက်စပ်မှု ရှိသောကြောင့် မှန်ကန်သော ဆိုးဆေးကို ရွေးချယ်ခြင်းသည် ဆိုးဆေး၏ အကောင်းဆုံး အကျိုးသက်ရောက်မှုကို သေချာစေပါသည်။
အသုံးများသော ဆေးဆိုးခြင်းနည်းလမ်းများတွင် အရည်ပျော်ဆေးဆိုးခြင်းနှင့် တိုက်ရိုက်ဆေးဆိုးခြင်း ပါဝင်သည်။ အရည်ပျော်ဆေးဆိုးခြင်းသည် များသောအားဖြင့် polyester အမျှင်များကဲ့သို့သော ဓာတုအမျှင်များအတွက် သင့်လျော်သည်။ ဤနည်းလမ်းသည် ဆိုးဆေးကို သွန်းသောအခြေအနေသို့ အပူပေးကာ တူညီသောဆေးဆိုးခြင်းအကျိုးသက်ရောက်မှုရရှိရန် အမျှင်အတွင်းသို့ ထိုးဖောက်ဝင်ရောက်နိုင်စေပါသည်။ Direct dyeing သည် ဆိုးဆေးကို ဖိုက်ဘာ မျက်နှာပြင်သို့ တိုက်ရိုက် လိမ်းခြင်း ဖြစ်သည်။ ၎င်းသည် အချို့သော သဘာဝအမျှင်များအတွက် သင့်လျော်ပြီး စွမ်းအင်ကို ချွေတာပြီး အပူချိန်နိမ့်သောနေရာတွင် ဆေးဆိုးနိုင်သည်။
ဆေးဆိုးခြင်းလုပ်ငန်းသည် အထည်၏အသွင်အပြင်ကို မြှင့်တင်ပေးရုံသာမက ချောထုတ်ကုန်၏ အရောင်၊ အရောင်အကြည်နှင့် တောက်ပမှုအပေါ်တွင် အရေးပါသော သက်ရောက်မှုရှိသည်။ အရောင်မြန်ခြင်း၏စွမ်းရည်ကိုရည်ညွှန်းသည်။ဆေးဆိုးထည်အဝတ်လျှော်ခြင်း၊ ပွတ်တိုက်ခြင်းနှင့် အလင်းရောင်ကဲ့သို့သော ပြင်ပပတ်ဝန်းကျင်အောက်တွင် ၎င်း၏အရောင်ကို ထိန်းသိမ်းရန်။ အရောင်စွဲမြဲမှုသည် အသုံးပြုနေစဉ်အတွင်း အထည်၏ တာရှည်ခံမှုနှင့် လှပမှုကို သေချာစေသည်။ ထို့အပြင်၊ ဆေးဆိုးခြင်းလုပ်ငန်းစဉ်အတွင်း တောက်ပမှုသည် အထည်၏ အလုံးစုံအမြင်အာရုံအကျိုးသက်ရောက်မှုကိုလည်း ထိခိုက်စေပါသည်။ ခိုင်ခံ့တောက်ပသော အထည်များသည် အများအားဖြင့် ပိုမိုမြင့်မားပြီး ဆွဲဆောင်မှုရှိသောပုံပေါက်သည်။
ဆေးဆိုးခြင်းလုပ်ငန်းတွင် ဆိုးဆေးရွေးချယ်မှုသည် အရေးကြီးပါသည်။ ယေဘူယျအားဖြင့်၊ ဆေးဆိုးခြင်းလုပ်ငန်းတွင် အသုံးများသော ဆိုးဆေးများတွင် အရည်ပျော်ဆေး၊ တိုက်ရိုက်ဆိုးဆေးနှင့် အက်ဆစ်ဆိုးဆေးများ ပါဝင်သည်။ အရည်ပျော်သောဆိုးဆေးများသည် ဓာတုအမျှင်များအတွက် သင့်လျော်ပြီး တောက်ပသောအရောင်များကို ပေးစွမ်းနိုင်သည်။ တိုက်ရိုက်ဆိုးဆေးများအတွက်သင့်လျော်သည်။ချည်ထည်s နှင့်ကောင်းမွန်သောအရောင်စွမ်းဆောင်ရည်ရှိသည်; အက်ဆစ်ဆိုးဆေးကို သိုးမွှေးနှင့် ပိုးထည်အတွက် အဓိကအသုံးပြုသော်လည်း အရောင်အသွေး ကြွယ်ဝပြီး တောက်ပမှုကိုပေးစွမ်းနိုင်သော အထည်များဖြစ်သည်။ အထည်၏ပစ္စည်း၊ အသုံးပြုမှုပတ်ဝန်းကျင်နှင့် နောက်ဆုံးထုတ်ကုန်၏နေရာချထားမှုတို့ကို အခြေခံ၍ တိကျသော ဆိုးဆေးရွေးချယ်မှုကို ကျယ်ကျယ်ပြန့်ပြန့် ထည့်သွင်းစဉ်းစားရန် လိုအပ်ပါသည်။
4. သပ်ရပ်ပြီး စီမံဆောင်ရွက်ပေးခြင်း။
ဆေးဆိုးပြီးနောက်၊ အထည်သည် အချောထည်ပြုလုပ်သည့် လုပ်ငန်းစဉ်သို့ ရောက်ရှိလာသည်၊၊ ယင်းသည် အထည်၏ အကောင်းဆုံးကုန်ချောအကျိုးသက်ရောက်မှုကို ရရှိစေရန်အတွက် အရေးကြီးသောအဆင့်တစ်ခုဖြစ်သည်။ အချောသတ်ခြင်းလုပ်ငန်းစဉ်တွင် အများအားဖြင့် အရွယ်အစား၊ လှိမ့်ခြင်း၊ အခြောက်ခံခြင်းနှင့် ပြက္ခဒိန်ပြုလုပ်ခြင်းကဲ့သို့သော လင့်ခ်များစွာပါဝင်ပြီး ၎င်းတို့တစ်ခုစီသည် အထည်၏နောက်ဆုံးအရည်အသွေးနှင့် အသွင်အပြင်တွင် အရေးပါသောအခန်းကဏ္ဍမှ ပါဝင်ပါသည်။
ပထမဦးစွာ၊ အရွယ်အစားသည် အပြီးသတ်ခြင်း၏ပထမအဆင့်ဖြစ်ပြီး အဓိကရည်ရွယ်ချက်မှာ အရွယ်အစားထည့်ခြင်းဖြင့် အထည်၏တောင့်တင်းမှုနှင့်တောက်ပမှုကို မြှင့်တင်ရန်ဖြစ်သည်။ ရွေးချယ်မှုနှင့်အရွယ်အစားပမာဏသည်အထည်၏ခံစားချက်နှင့်အသွင်အပြင်ကိုတိုက်ရိုက်အကျိုးသက်ရောက်လိမ့်မည်။ သင့်လျော်သောအရွယ်အစားအထည်ကိုလုပ်ပါ။ပိုမိုတောင့်တင်းခြင်း၊ အရေးအကြောင်းများကို လျှော့ချပေးပြီး အလုံးစုံ အမြင်အာရုံကို မြှင့်တင်ပေးခြင်း။
နောက်တစ်ခုကတော့ နောက်ဆက်တွဲ သိုလှောင်မှုနဲ့ သယ်ယူပို့ဆောင်ရေးအတွက် အဓိကအားဖြင့် အထည်ကို သေသပ်စွာ လှိမ့်ပေးမယ့် rolling process ဖြစ်ပါတယ်။ လှိမ့်ခြင်းလုပ်ငန်းစဉ်အတွင်း၊ အော်ပရေတာသည် အထည်၏ချောမွေ့မှုကိုသေချာစေရန်၊ အထည်၏သပ်ရပ်လှပနေစေရန်အတွက် အရေးအကြောင်းများနှင့် ပုံပျက်ခြင်းများကိုရှောင်ရှားရန် လိုအပ်သည်။
အခြောက်ခံခြင်းသည် အထည်၏ အစိုဓာတ်ကို ဖယ်ရှားရန်နှင့် နောက်ဆက်တွဲအသုံးပြုရာတွင် ၎င်း၏ တည်ငြိမ်မှုနှင့် တာရှည်ခံမှုကို သေချာစေရန် ရည်ရွယ်ချက်မှာ ပြီးမြောက်ခြင်းအတွက် မရှိမဖြစ်လိုအပ်သော အဆင့်တစ်ခုဖြစ်သည်။ အခြောက်ခံချိန်နှင့် အပူချိန်တို့ကို ချိန်ညှိရန် လိုအပ်ပါသည်။အထည်၏ပစ္စည်းအပူချိန်အလွန်အကျွံကျုံ့ခြင်း သို့မဟုတ် ပျက်စီးယိုယွင်းခြင်းမှ ကာကွယ်ရန်။
နောက်ဆုံးတွင်၊ calendering သည် ၎င်း၏တောက်ပမှုနှင့် ခံစားမှုကို ပိုမိုကောင်းမွန်စေရန်အတွက် စက်ကိရိယာများမှတစ်ဆင့် အထည်များကို ပြားချပ်စေသည့်လုပ်ငန်းစဉ်ဖြစ်သည်။ Calendering သည် အထည်၏မျက်နှာပြင်ကို ချောမွေ့စေရုံသာမက ၎င်း၏အမြင်အာရုံကို ဆွဲဆောင်မှုအားကောင်းစေကာ ပြီးသွားသောအထည်ကို ပိုမိုအဆင့်မြင့်သည့်အသွင်ဖြစ်စေသည်။
5.Finished ထုတ်ကုန်အပြောင်းအလဲနဲ့
နောက်ဆုံးတွင်၊ ထိုးပြီးသောအထည်ကို ပြီးသောအခါ၊ ၎င်းသည် အထည်၏ အလုံးစုံဖွဲ့စည်းပုံနှင့် အရည်အသွေးကို မြှင့်တင်ရန် အဓိကသော့ချိတ်တစ်ခုဖြစ်သည့် ထုတ်ကုန်အချောထည်လုပ်ငန်းစဉ်အဆင့်သို့ ရောက်ရှိသည်။ ထုတ်ကုန်အချောထည်ပြုလုပ်ခြင်းတွင် အဓိကအားဖြင့် ပုံနှိပ်ခြင်းနှင့် ပူသောတံဆိပ်ရိုက်ခြင်းကဲ့သို့သော အထူးလုပ်ဆောင်ခြင်းနည်းပညာများပါဝင်ပြီး အထည်အတွက် အမြင်အာရုံကို ဆွဲဆောင်နိုင်ရုံသာမက ၎င်း၏စျေးကွက်ပြိုင်ဆိုင်မှုကိုလည်း မြှင့်တင်ပေးနိုင်ပါသည်။
ပထမဦးစွာ၊ အချောထည်သည် အဓိကအားဖြင့် အထည်၏ ပုံသဏ္ဍာန်နှင့် ပုံသဏ္ဍာန်ပြုလုပ်ခြင်းတွင် အဓိကအားဖြင့် ထုတ်ကုန်အချောထည်ပြုလုပ်ခြင်း၏ အရေးကြီးသော အစိတ်အပိုင်းတစ်ခုဖြစ်သည်။ ဤလုပ်ငန်းစဉ်အားဖြင့်၊ အထည်၏မျက်နှာပြင်သည်ပိုမိုချောမွေ့လာပြီး၊ အရေးအကြောင်းများနှင့်ပုံမှန်မဟုတ်သောအနားများကိုဖြတ်တောက်ပြီး၎င်းကိုပိုမိုသပ်ရပ်ပြီးပရော်ဖက်ရှင်နယ်အသွင်အပြင်ဖြစ်စေသည်။ Calendering သည် အထည်၏ အရောင်တောက်ပမှုကို သိသာထင်ရှားစွာ မြှင့်တင်ပေးနိုင်ပြီး ၎င်းကို ပိုမိုမြင့်မားသောအသွင်အပြင်နှင့် ဝယ်ယူလိုသော စားသုံးသူများ၏ ဆန္ဒကို မြှင့်တင်ပေးပါသည်။
ပုံနှိပ်ခြင်းဆိုသည်မှာ ချည်ထည်အချောထည်များ ပြုလုပ်ရာတွင် အသုံးများသော အထူးလုပ်ငန်းစဉ်တစ်ခုဖြစ်သည်။ ပုံနှိပ်ခြင်းမှတဆင့်၊ အမျိုးမျိုးသောပုံစံများနှင့် အရောင်များကို အထည်များတွင် ထည့်သွင်းနိုင်သည် ပုံနှိပ်ခြင်းနည်းပညာတွင် စခရင်ပုံနှိပ်ခြင်း၊ ဒစ်ဂျစ်တယ်ပုံနှိပ်ခြင်းနှင့် အပူလွှဲပြောင်းခြင်း အပါအဝင် ပုံစံများစွာရှိပြီး ၎င်းတို့တစ်ခုစီတွင် ၎င်း၏ကိုယ်ပိုင်ထူးခြားသောအကျိုးသက်ရောက်မှုများနှင့် အသုံးချမှုနယ်ပယ်များရှိသည်။ ပုံနှိပ်ခြင်းသည် အထည်၏ အလှကို မြှင့်တင်ရုံသာမကဘဲ စျေးကွက်၏ စိတ်ကြိုက်ဖန်တီးမှုနှင့် ကွဲပြားမှုများအတွက် လိုအပ်ချက်ကို ဖြည့်ဆည်းပေးကာ စားသုံးသူများ၏ အာရုံစိုက်မှုကို ပိုမိုရရှိစေပါသည်။
Hot stamping ဆိုသည်မှာ အာရုံခံစားမှုကို ပေါင်းထည့်နိုင်သော လုပ်ငန်းစဉ်တစ်ခုဖြစ်သည်။ဇိမ်ခံထည်ဝါ. သတ္တုပြား သို့မဟုတ် အထည်၏မျက်နှာပြင်ပေါ်တွင် အထူးအလွှာကို လိမ်းခြင်းဖြင့်၊ ပူနွေးသောတံဆိပ်ခတ်ခြင်းသည် တောက်ပသောအကျိုးသက်ရောက်မှုကို ဖန်တီးနိုင်ပြီး အထည်ကို အလင်းရောင်အောက်တွင် ထူးထူးခြားခြားတောက်ပစေသည်။ ဤလုပ်ငန်းစဉ်သည် ထုတ်ကုန်များ၏ တန်ဖိုးနှင့် စျေးကွက်အနေအထားကို သိသာထင်ရှားစွာ မြှင့်တင်ပေးနိုင်သည့် အဆင့်မြင့်အဝတ်အစားများနှင့် ဖက်ရှင်အသုံးအဆောင်များတွင် အသုံးပြုလေ့ရှိသည်။
ထို့အပြင်၊ ထုတ်ကုန်အချောထည်ပြုလုပ်ခြင်းတွင် ရေစိုခံခြင်း၊ အရေးအကြောင်း ဆန့်ကျင်ခြင်း၊ ဘက်တီးရီးယားပိုးမွှားများနှင့် အခြားလုပ်ဆောင်မှုဆိုင်ရာ လုပ်ဆောင်မှုကဲ့သို့သော အထူးကုသနည်းများလည်း ပါဝင်နိုင်ပြီး၊ ၎င်းသည် အထည်၏ လက်တွေ့ကျမှုနှင့် သက်တောင့်သက်သာရှိမှုကို ပိုမိုမြှင့်တင်ပေးနိုင်သည့်အပြင် ကွဲပြားခြားနားသော စားသုံးသူများ၏ လိုအပ်ချက်များကို ဖြည့်ဆည်းပေးနိုင်မည်ဖြစ်သည်။
အထက်ဖော်ပြပါ အဆင့်ငါးဆင့်ကို ပြီးမြောက်ပြီးနောက်၊ အရေအတွက်သည် ဖောက်သည်လိုအပ်ချက်များနှင့် ကိုက်ညီကြောင်း သေချာစေရန် ကျွန်ုပ်တို့၏အထည်များကို လှိမ့်စစ်ဆေးခြင်းများ ပြုလုပ်လေ့ရှိပါသည်။ ဤလုပ်ငန်းစဉ်သည် ရိုးရှင်းသောပမာဏစစ်ဆေးရုံသာမက အထည်၏အရည်အသွေးကို ကျယ်ကျယ်ပြန့်ပြန့်စစ်ဆေးခြင်းလည်း ပါဝင်သည်။ အထည်လိပ်တစ်ခုစီသည် ကျွန်ုပ်တို့၏စံနှုန်းများနှင့် ဖောက်သည်များ၏မျှော်လင့်ချက်များနှင့်ကိုက်ညီကြောင်း သေချာစေရန်အတွက် အထည်၏အရောင်၊ အသား၊ အထူစသည်တို့ကို ဂရုတစိုက်ကြည့်ရှုပါမည်။ ထို့အပြင်၊ အချို့သောဖောက်သည်များသည် ကျွန်ုပ်တို့၏အထည်များကို ပိုမိုတင်းကြပ်စွာစမ်းသပ်ရန် လိုအပ်ပါလိမ့်မည်။ ဤစစ်ဆေးမှုများတွင် ရုပ်ပိုင်းဆိုင်ရာစွမ်းဆောင်ရည်စမ်းသပ်ခြင်း၊ ဓာတုဗေဒပါဝင်မှုခွဲခြမ်းစိတ်ဖြာခြင်းနှင့် တာရှည်ခံမှုအကဲဖြတ်ခြင်းတို့ ပါဝင်နိုင်သည်။ ကျွန်ုပ်တို့၏ဖောက်သည်များ၏လိုအပ်ချက်များကိုဖြည့်ဆည်းရန်အတွက်အထည်များသည်နယ်ပယ်ပေါင်းစုံတွင်စက်မှုလုပ်ငန်းစံနှုန်းများနှင့်ကိုက်ညီကြောင်းသေချာစေရန်ပရော်ဖက်ရှင်နယ်စမ်းသပ်အေဂျင်စီများနှင့်ပူးပေါင်းဆောင်ရွက်လေ့ရှိပါသည်။ ၎င်းသည် ကျွန်ုပ်တို့၏ထုတ်ကုန်များအပေါ် ဖောက်သည်များ၏ယုံကြည်မှုကို မြှင့်တင်ပေးရုံသာမက စျေးကွက်တွင် ကျွန်ုပ်တို့၏ယှဉ်ပြိုင်နိုင်စွမ်းအတွက် ခိုင်မာသောပံ့ပိုးမှုလည်းပေးပါသည်။ ၎င်းသည် ကောင်းမွန်သော အမှတ်တံဆိပ်ပုံသဏ္ဍာန်ကို ထူထောင်ရန်နှင့် ဖောက်သည်များ ပိုမိုနှစ်သက်မှုကို ရရှိရန် အရေးကြီးသော အခန်းကဏ္ဍမှ ပါဝင်ပါသည်။
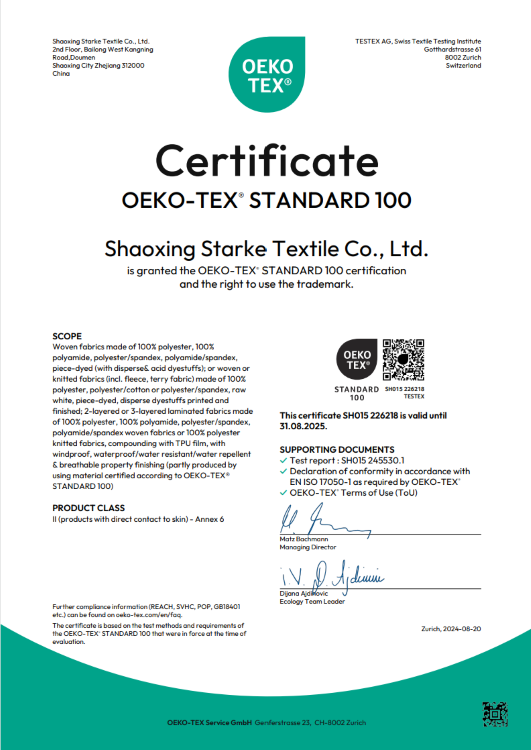
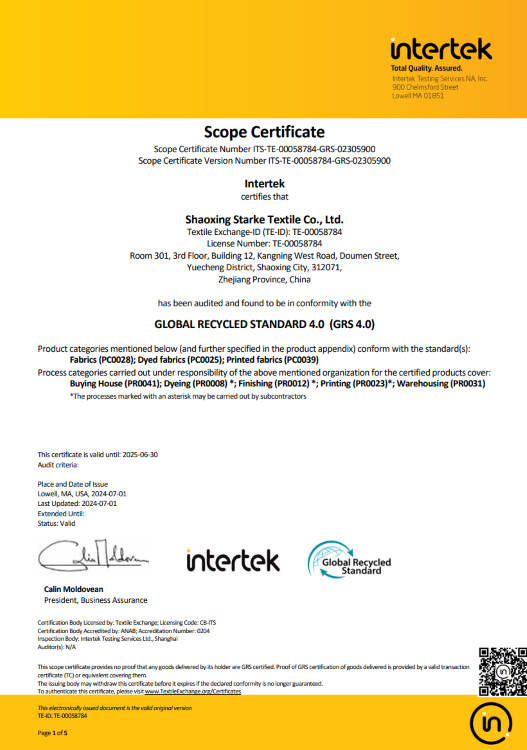